FASTENERS WITH JR2000 COATING
WHAT IS THE JR2000 COATING?
The JR2000 coating is a type of ZnNi alloy that offers exceptional cathodic protection against corrosion. It is applied through an alkaline electrolytic process and is capable of withstanding temperatures of up to 150°C.
The JR2000 Top Coat applied by SNK offers a sealing layer with organic-mineral characteristics, providing heightened anti-corrosion protection to the component and also adjusting it to a specific friction coefficient.
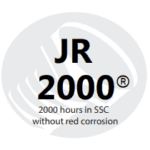
SPECIFIC APPLICATIONS OF JR2000
This coating is particularly useful in industrial applications that require high corrosion resistance and robust thermal resistance.
Some of the most common applications include automobile manufacturing, machinery, aeronautics, solar trackers, silos, and greenhouses.
THE JR2000 COATING + JR2000 PASSIVATION + JR2000 TOP COAT IS USED IN A WIDE RANGE OF COMPONENTS, SUCH AS:
Threaded fasteners that require high corrosion and thermal resistance, such as temperature-loaded joints up to 150°C in engine compartments of vehicles and brakes, as well as chassis joints.
Pipe connection accessories like fittings, bushings, flanges, hydraulic valves in hydraulic systems.
Joints that require electrical conductivity.
Rubber-to-metal bonding applications.
Steel fasteners in contact with aluminum.
JR 2000 - LATEST GENERATION ZINC/NICKEL PROCESS
- Modular additive system, adapted to the needs of the renewable energy market.
- Excellent thickness distribution.
- High tolerance to burn-through.
- Very high electrolytic performance, with a high and stable deposition rate.
- High temperature tolerance.
- Slow aging of electrolytes. Possibility of complete regeneration without dilutions.
- High tool abrasion resistance (550HV).
PROPERTIES OF THE JR2000 COATING
Additionally, according to neutral salt spray chamber corrosion resistance tests (ISO 9227), the JR2000 combined with the JR2000 passivation and JR2000 top coat can achieve up to 2000 hours before the appearance of red corrosion.
THE JR2000 COATING OFFERS THE FOLLOWING PROPERTIES:
Thermal shock resistance (300°C for ½ hour and cooled in water at 20°C without detachment)
Silver appearance with high scratch resistance.
Good electrical conductivity.
Medium weldability.
High-temperature resistance (up to 150°C).
Medium ductility.
Good tool abrasion resistance.
El proceso de aplicación del recubrimiento JR2000 se realiza en un sistema de tambor.
Las piezas metálicas
The JR2000 coating application process is carried out in a drum system.
The metal parts are deposited in an alkaline ZnNi electrolyte with a contribution of 12% to 15% Ni. Subsequently, the transparent JR2000 passivation is applied, which protects the coating from white corrosion. Finally, the JR2000 top coat penetrates the passivation and seals the microcracks and pores, ensuring complete protection against corrosion, improving the aesthetic appearance, and increasing the surface hardness of the coating.
In conclusion, the JR2000 coating is an excellent choice for those looking for robust corrosion protection in high-demand industrial applications. With its ability to withstand high temperatures, good electrical conductivity, medium ductility, medium weldability, and tool abrasion resistance, this coating is a reliable option for a wide range of applications.